|
The project consists of the design, construction, testing, and optimization of a pilot plant for the conversion of biomasses into fuel gas (syngas). This pilot plant has been built in the F.lli Fragola S.p.A. factory and will be installed and tested in the coming days.
The processing potential has been established at 200 Kg/h of incoming biomass. The basic processes of the plant are “pyrolysis” and “gasification”.
Pyrolysis is the high-temperature transformation of biomass, typically at 350-600°C and in the absence of oxygen, into volatile, liquid and solid carbonaceous compounds.
Afterwards these compounds are transferred to the gasification zone where, by means of a high-temperature air injection of a specific quantity, an incomplete combustion (in the absence of oxygen), and other more complex chemical reactions, they are transformed almost totally into gas, leaving an ash residue totaling less than 5% of the weight of the incoming substances.
After filtrations, passing through heat recovery systems, coolings, and storage in holding tanks, the gas produced – which has a calorific value of around 4000 Kcal/m3, around half that of natural gas – will be used in a controlled-ignition endothermic engine which, coupled with an alternator, will produce around 150 kWh of electricity
DETAILED DESCRIPTION OF THE PROCESS AND ITS STAGES
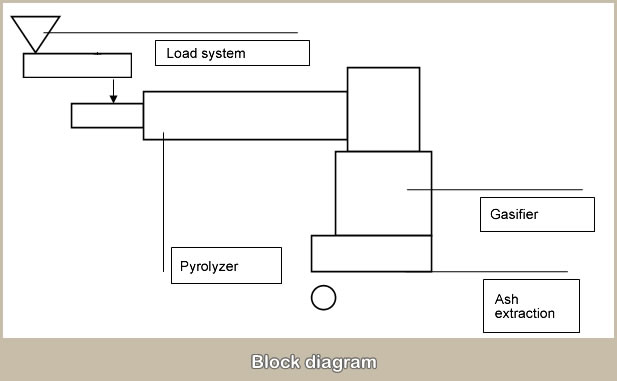
BLOCK DIAGRAM
The pilot plant will be made up of the following elements: 1) Loading system 2) Pyrolyzer 3) Gasifier 4) Ash removal system
The loading system will consist of a screw conveyor equipped with a storage hopper, which feeds a device that transfers the biomass into the pyrolyzer, with a separation of the internal and external zones to prevent the leaking of the gas from inside the pyrolyzer, which is in a state of slight overpressure, and to prevent the entrance of air together with the biomass. There will be level, temperature, and pressure sensors in this element for the continuous monitoring of these values.
The pyrolyzer consists of a horizontal conveyor equipped with a rotating internal reel with Archimedean spirals and paddles for pushing forward and mixing the loaded material, and an external cylindrical container, heated with the hot gas produced by the gasifier, for transferring the heat to the biomass, and insulated against the external environment. In this stage, also, there will be sensors similar to those of the preceding module installed in various positions, for monitoring and controlling the process.
The gasifier has a vertical axis cylinder with a middle part made of materials that resist temperatures of over 1000°C, and in the zones with relatively lower temperatures, of special steels. At various heights of the cylinder will be installed distribution toruses which, by means of nozzles, will convey very hot air into the biomass, already transformed by the pyrolysis, to achieve the gasification. This whole section will be insulated both inside and out, and instruments have been installed at various heights for measuring temperature and pressure. Based on the data acquired through the control and adjustment system, it is possible to modulate the quantity of air to be sent to each single hot air distribution torus, so the gasification process can be optimized. In addition to the hot air, water vapor of specific quantities will also be injected into this section in order to increase the percentage of fuel gas in the mix of gases produced, and also to regulate the internal temperature of the gasifier.
The ash removal system is positioned in the lower part of the gasifier, and is responsible for supporting the material to be gasified, permitting the generated gas to flow out, and collecting the ash, limiting its entrainment into the gas. This stage will have a catalytic transformation module for the tarry fractions present in the hot gas. The gas coming out of this stage will be conveyed to heat recovery, while the ash will go through a transfer device with its internal and external zones separated, similar to the initial entrance section, but smaller in size.
Aims and objectives
Our design must solve two problems that have remained unsolved up to now:
a) treatment of non-homogeneous fuels b) creation of medium-size and small plants.
To accomplish this we have combined in a single machine two different techniques, which up to now have been used separately and distinctly: pyrolysis and gasification. The separate initial pyrolysis will make it possible to treat the fuel and render it uniform before entering the gasifier, in order to minimize
|
|
|